生産プロセス
ホーム > 生産プロセス > 詳細
解析
流動解析ソフト JSCAST を駆使し最適な鋳造方案の実現
ゲート位置・点数およびオーバーフロー位置・点数を解析により未充填、湯流れ不良、充填負荷が大きい部分を見つけ良好な湯流れを実現するまで検討を重ね改良を行います。
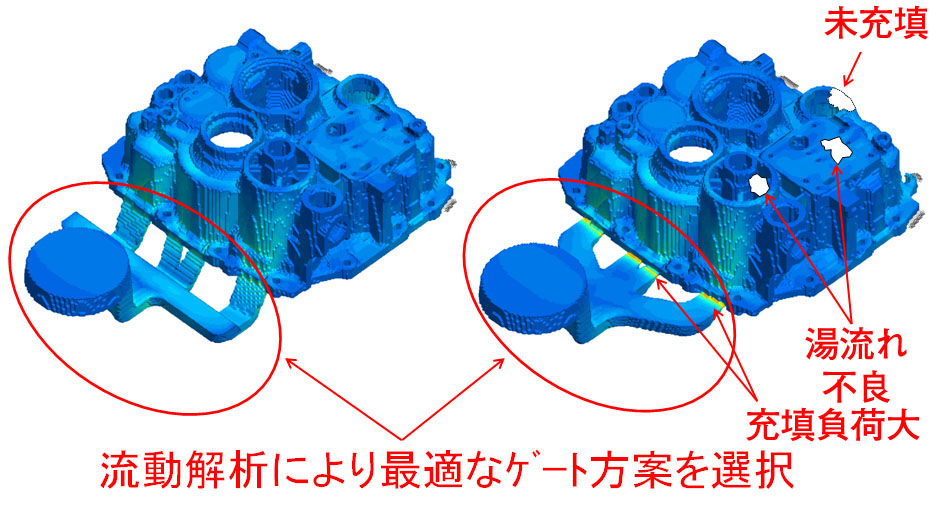
鋳造
大型アルミダイカスト製品の事業
- 弊社独自のダウンサイジング技術の確立により、650ton鋳造機により最大のもので製品平面サイズ450mmx450mm程度、製品重量4kg程度(一般的に800tonで鋳造する大きさ)を鋳造します。
- さらなる大物ダイカスト製品対応に向け 2015年8月800ton鋳造機1台導入。
このマシンにおいてもダウンサイジング技術投入し2015年後半の目標は1000tonクラスの製品を800tonで鋳造。
精密ダイカスト製品の技術構築
他鋳造メーカーが避ける難易度の高い製品へも挑戦しています。
-
- エンジン部品(テンショナー)
- 型トラブルが発生しやすいことから他社では採用例が少ない斜目穴構造を金型へ盛り込み、量産化に成功し鋳巣低減に大きな効果が出ています。
-
- バイク用リモコンカバー
- ダイカスト金型(70mmx15mmサイズ製品)において、樹脂金型同様のアンダーカット構造にて量産化に成功しています。
-
- 鍵部品
- 金型薄入子(約1mm厚)の重ね合わせ構造により、鍵穴形状を実現しています。
機械加工
品質管理体制の充実
弊社では次の様な体制により品質管理の充実をはかっています。
- ●「加工品検査場」の拡張
- ●検査器具の見直し(ピンゲージ1200本・デジタル測定器・他導入)
- ●マシニングセンターによる自動測定検査の導入
- ●「鋳造班」「金型班」に対する素早い情報のフィードバック
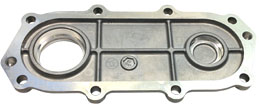
例)一貫生産での情報共有による品質の向上
ミッションケース用部品(アルミダイカスト)
平面加工・h7公差穴加工・ベアリング圧入部切削加工
- 問題:歪によるクロカワ(削り残り)の発生
解決:鋳造時の最適な条件を追及するため、歪の検具を社内製作 - 問題:加工面に出る鋳巣の問題
解決:鋳造と加工を同時に行い、リアルタイムな鋳造条件出し
これら対応により、初品による鋳造での不良率が7%から1%以下へ早期に削減!
航空部品加工技術
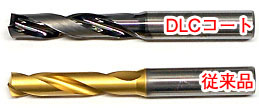
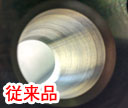
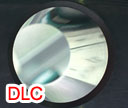
アルミダイカスト用刃物へ最新のコーティング技術(ダイヤモンド・ライク・カーボンコーティング)通称「DLC」コートとも言うこのコーティング技術を施すことで従来の加工速度の約1.5倍以上の切削速度と、約2倍以上の耐久性により安定した精密加工が可能となります。
この「DLC」工具を最大限に発揮させるべく、最新の高速加工設備を完備しさらに、経験ある技術者による半導体関連部品の精密加工技術を投入しております。
3次元加工技術
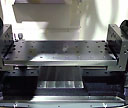
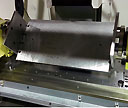
インデックステーブルによる高速多面加工
あらゆる角度からの加工に対応することができ、大型製品の付替え時間も大幅にカットする事が可能となります。
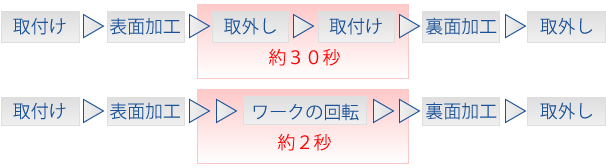
生産能力の拡大

設備増強に対応するためMC/NC加工班の製造場所を移転し今までの約3倍に拡大しまたした。
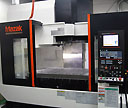
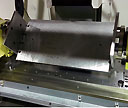
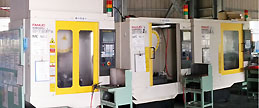
大型化への対応および量産体制の構築
大型マシニングセンター(全長1,050mmに対応)を新たに追加投入し大型用インデックステーブル(4面加工設備)と大型製品対応のロボドリル(全長700mmに対応)も追加導入。
これにより生産能力を約35%、年間生産能力を約15万台から約30万台へアップ。
アルミダイカストマシン800tの量産加工に完全対応。
精密加工への対応
当社では工程内検査成績表の導入を行っております。
例)検査時、公差限界値ギリギリの測定結果が出た場合
- 製品の遡り検査を行い、NGの際は対象ロットを隔離
- 混入を防ぐため赤色の識別用紙を投入後、全数検査
- 同時に品質保証部への報告
- 検査表に製品評価と詳しい内容を記入
- 加工機の刃物交換や工具調整により中間公差へ補正
コストダウン
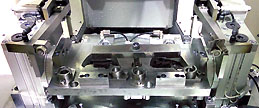
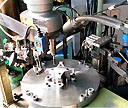
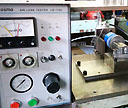
当社の加工班は生産技術班としての役割も行っており、従来のマシニングセンターでの加工だけに留まらず、加工専用機の設計及び製作や、可動式加工治具、リークテスト検査装置等、あらゆる技術によりコストダウンを追及しております。
また自動クランプ及び未加工防止機能等、マシニングセンター本体で制御する機構を取り入れた加工を行っています。
今後に措いては、ハンドロボットの導入による無人での加工や、画像検査装置の導入も計画し準備を進めております。
検査・納品
初期管理計画
各帳票類作成
QC工程表や作業標準書・検査基準書などの各種標準書・基準書を作成いたします。
工程故障モード影響解析(工程FMEA)
工程FMEAにより事前に問題点を予測・抽出し改善に役立てます。
製品評価
図面規格全寸法検査や破壊試験などにより製品評価を行います。
工程内検査
工程内検査(鋳造)
- 寸法(穴径、厚み、位置精度、面精度等をノギス、ピンゲージ、検査ジグにて評価)
- 外観(打痕、キズ、湯ジワ)
工程内検査(加工)
-
寸法確認(下記測定機器で評価)
- 内径マイクロ
- デプスゲージ
- ピンゲージ
- ノギス
- ハイトゲージ
- 加工部確認
- ムシレ、段差
- 巣
- 湯じわ
出荷検査(最終検査)
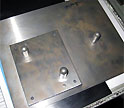
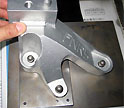
- 寸法(穴径、厚み、位置精度、面精度等をノギス、ピンゲージ、検査ジグにて評価)
- 外観(打痕、キズ、湯ジワ、表面処理有無)